BASED ON LATEST GENERATION GALVANIC SYSTEM
This plant offer the utmost precision and rapidity, to ensure the perfect and constant reproduction of inimitable, unique specimens of nickel plates.
Very latest improved model, with microprocessor controlled voltage increase, especially developed for the new sulphamate nickel bath “Speed”, with continuous filtration, two reciprocating cathode rods and bath agitation.
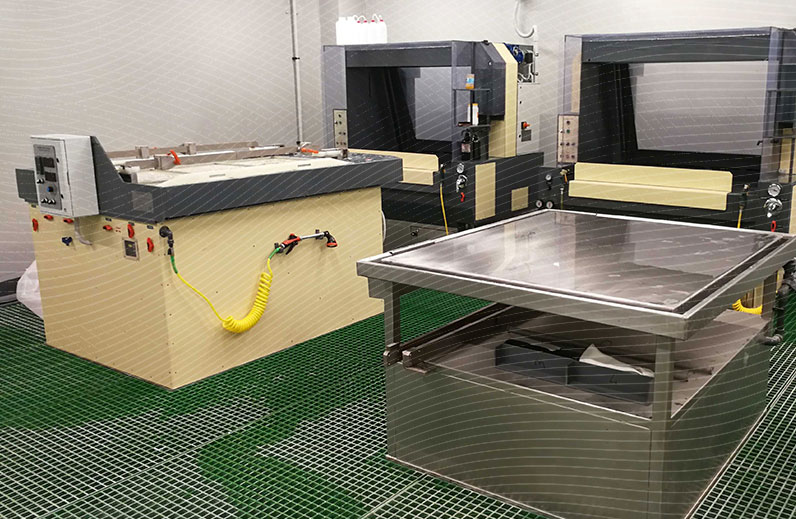
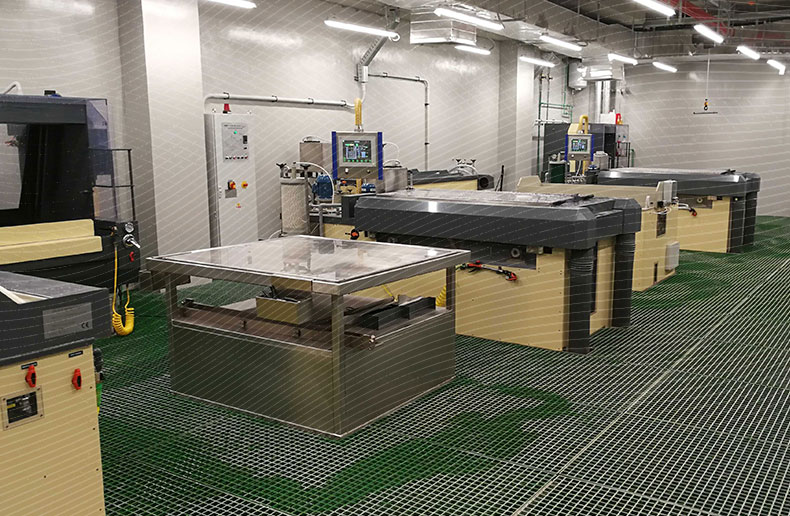
- High-speed nickel plating baths
- Hard chromium plating baths
- Electric current rectifiers for galvanic process
- Electroforming jigs
- Air scrubbers
- Industrial de-mineralisers
Due to the highly specialised nature of this equipment, it is of vital importance that the auxiliary devices and material employed are perfectly tuned to its requirements. All complementary items for this type of equipment have been selected carefully to guarantee ultimate performance results.
The above-indicated performance values refer to a production environment using recommended auxiliary items. These values may differ if the customer decides to use auxiliary items and/or material from other sources.
• Steel plate main tank with interstice, 5 mm thick inner ebonite lining and externally faced with shock resistant PVC cover plates. It is divided into a working compartment and a temperature regulation compartment by means of a removable plastic board. The temperature control is effected by an immersed PVDF (polyvinylidene fluoride) coil of which the inlet and outlet pieces are connected to an automatic temperature control unit in closed circuit. Total exchange surface of the coil: 3.5 m2.
This temperature control unit comprises:
– circulation pump
– magnetic valve
– heat exchanger to be connected to a chilled water supply
– electrical heater 20 kW
– expansion tank
– security thermostat
• Two measuring probes together with the thermo-resistance are positioned on the PVC plate and provide for the automatic regulation of the heating and cooling as well as for the automatic interruption of all circuits whenever the temperature rises above the preselected maximum temperature. The measuring probes are connected to the PLC and displayed on the Touchscreen panel. The working compartment is fitted with slanting bottom, discharge pipe and removable quadripartite cover made of shock resistant PVC.
• Filter tank welded directly to one of the short sides of the main tank. The electrolyte flows from the temperature regulation compartment via an overflow baffle directly into the filter tank. The latter is equipped with a plastic cover plate supporting the agitator, the electrode holder, the pH-meter electrodes, the immersion pump plus the automatic, electronic, maximum, minimum and working level regulator controlling the magnetic valve for the admission of deionised water.
• Bath agitation with injected air by means of two PVC pipes which are attached to the two removable diaphragm panels. Air is provided by an oil free blower (included).
• A stainless steel bracket laterally attached to the main tank, carries the filter press wholly manufactured from transparent acrylic material and containing 30 exchangeable polypropylene filter disks.
• An additional PVC bracket fastened to the upper tank rim adjacent to the filter bracket enables the filter elements to be deposited when the paper filtering disks are changed.
• Two hinged stainless steel footbridges are fitted to the external PVC boards on the two longitudinal sides of the working tank.
• A further stainless steel bracket below the filter tank accommodates a divided PVC collecting vat for receiving any over-flowing electrolyte and for preparing the activated carbon.
• A magnetically-driven auxiliary pump, free of any seals, located underneath the PVC collecting vat serves the purpose of periodically depositing the filter aid and the activated carbon on the filter medium. By means of the connecting sleeves supplied with the tank, the pump may also be used for the complementary bath filtration.
• During the normal processing cycle, the immersion pump provides for the electrolyte to be pumped from the filter tank through the filter press and subsequently through a combined plastic and armoured rubber pipe back into the working compartment at the side opposite the overflow. From the working compartment the electrolyte penetrates into the separate temperature regulation compartment and finally flows back again into the filter tank via the overflow lip.
• A flanged gear motor, combined with an eccentric disk, controls the reciprocating movement of a trolley made of copper and stainless steel running on ball bearing Arnite rollers, located outside the bath. Two easily adjustable, flat copper work rods 60 x 15 mm are supported by the frame. They are each equipped with a pair of clamps for the quick locking of the plate holding frames.
• Copper bus bar armature of rectangular section 80 x 24 mm, complete with 6 special titanium anode baskets of 1’220 x 150 x 50 mm each, 6 anode bags and 12 clamping screws.
• Anode compartment consisting of a central, U-shaped and PVC-HT rail of which the lower part acts as anode sludge collector and two polycarbonate diaphragm panels each covered with PP filtering cloth. These panels, perforated all over their peripheral area, serve as “current filter” and hence enable a uniform deposit to be obtained for both plates.
• Two PVC spray nozzles with regulating valves and connecting hoses for washing the nickel plates are provided on both sides of the reduction gear motor.
• Electric control cabinet equipped with PLC and connected to the bath and the corresponding rectifier.
• Touch screen terminal, installed on the bath by a rotating arm, showing all working parameters, i.e. DC voltage, current [A] (for each bar), bath temperature, pH value, and enabling all settings and commands for bath and rectifier. In particular, one screen page is for programming the automatic deposition through the following parameters: thickness, surface, current [A] (for each bar).
• The current pH value is displayed on the touch screen. The measure probe, directly mounted on the nickel tank, includes the following accessories:
– 1 PVC electrode holder
– 1 glass electrode pH complete with shielded flexible connecting lead, measuring range: 0 – 14 pH, temperature range: 0 – 70 degrees C
– 1 fully transistorised pH-meter amplifier with resistance Pt 100
• Two fume extractors, situated on the top length side, must be connected to a scrubber (this scrubber is not included in the supply and can be quoted separately)
• Electronic rectifier, high energy efficiency implements with switching technology, consisting of:
– Bridge diodes and IGBT transistors installed on the primary circuit.
– Power transformer with ferrite core magnetic circuit and litz wire for primary and secondary circuit.
– SHOTTKY diodes, inductor and capacitor, all installed on the secondary circuit for reduced output ripple. The output frequency is 32 KHz.